January 23rd "Marketing Your Turnings"
by Dave Dunn and Lyle Solem
|
Dave and Lyle discussing pricing of Larry's bowl
|
Dave Dunn and Lyle Solem's presentation at the January club meeting covered marketing our turnings.
Various outlets for selling our works were discussed including consignment shops, craft fairs, art cooperatives like the South Eastern Minnesota Visual Artists Gallery (SEMVA) and others as well as the advantages, disadvantages and costs associated with them.
|
Lyle reviewing identifying costs and calculating expected profits
|
Setting the price for a turning proved to be an exercise in determining market demand for a given audience (craft crowd, utilitarian, art, collector).
The ways in which the visual appeal of the design, the level of finish, 'hand feel' and many other factors both visual and tactile influence the price that could be charged for the piece was also discussed.
Once the price was set a comparison with true costs including time invested had to be made to get an idea of the profit of the proposed sales technique. We were reminded that bartering by potential customers or price reductions if the turning did not sell in a reasonable time period would change these numbers.
Dave ended the presentation with a reminder to never let the 'inside' of the turning become the 'outside' showing us a vase that can only be used for a very large kaleidoscope now that there is a hole in its bottom.
|
Show and Tell Pictures
|
|
February 27th "Inside-Out Turnings"
by Chuck Grimm
|
Chuck Grimm at work
|
Chuck Grimm's presentation at the February club meeting introduced 'inside-out' turnings.
The demo used a heart shaped candle holder to discuss the basic concepts behind an inside-out turning.
|
The turning of the inside of the candle holder was accomplished with these surfaces of the squares facing 'out'.
Chuck used screws to hold the blank together to avoid waiting for the glue to dry.
Chuck turing the inside facing out
|
After the inside was sanded and finished each of the two squares were rotated 180 degrees to expose the outside surface so it could be turned.
Chuck uses the 'shadow image' of the rotating blank to judge his cuts stopping the lathe periodically to inspect his progress.
Chuck recommends you take very light cuts with a freshly sharpened tool when
getting close to the final dimensions of the piece to minimize chip-out on the edges as well as keeping yourself from removing too much wood in any area.
Completed example
|
Show and Tell Pictures
|
|
ZVW Displays and Demonstrates at the 2014 Rochester Woodcarvers Show on March 22nd and 23rd.
Each year the Rochester Woodcarvers hold a two-day Woodcarvers Show in the 4 H building at the Olmsted Co. Fair Grounds to display their handiwork.
We thank the Rochester Woodcarvers for welcoming the Zumbro Valley Woodturners to join in this event to display our turnings, demonstrate on the lathe and educate the public in the art of woodturning.
Lyle Solem, Mike Schmidt and Chuck Grimm answering questions at our display table.
ZVW volunteers also demonstrated woodturning on our Club's small lathe. We turned honey dippers, holiday ornaments, finger tops, small bowls and other objects to give away to the crowd.
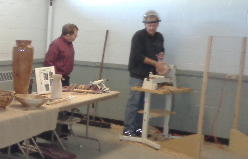 John Thorson turning a small bowl for someone
The Zumbro Valley Woodturners club donated several turnings to the collection of items on the raffle table that the crowd could bid on. All money collected in the raffle is used by the Rochester Woodcarvers to pay for this show, there was no attendance charge.
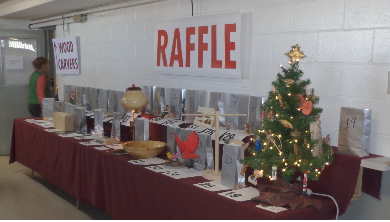 Raffle table at the Woodcarvers Annual Show
One of our club members, Chuck Grimm, gave away one of his hand-made lamps with a turned Boxelder lampshade. You may have to zoom in on this photo to see it in the center of the front row. This turning had a very full 'bid bag', very generous Chuck!
|
Our Volunteers at this Event
Lyle Solem and his wife Donna
Dale Eppen
Chuck Grimm
Mark Bherends
Mike Schmidt
John Thorson
Bob Post and his wife Karen
Dave Dunn
Jerry Huneke
A big thank you to Chuck Grimm who took on the organizational responsibility required to make this project a success for our club.
|
|